Dealing with Popular Difficulties in Automated Can Sealing Machine Operations
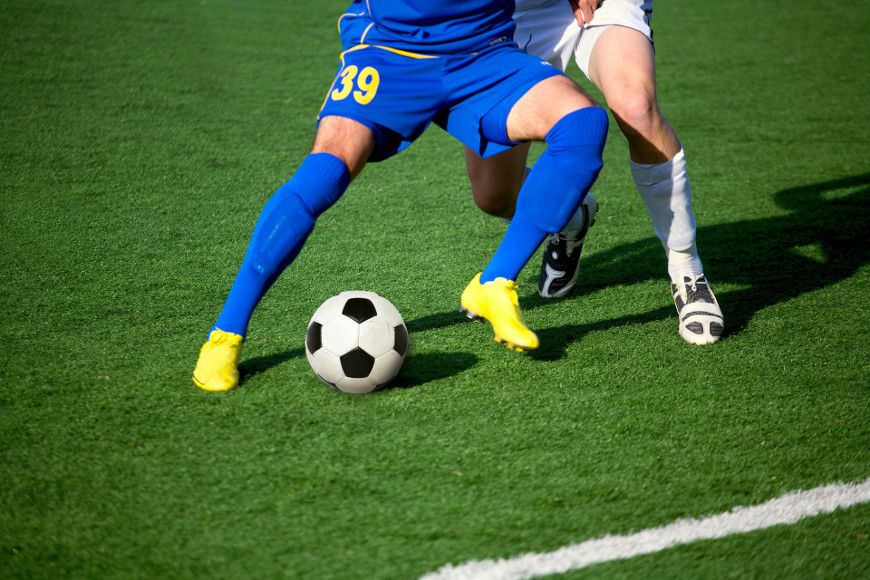
Intelligent can sealing devices are stylish pieces of equipment found in refreshment packaging procedures to guarantee the secure securing of lightweight aluminum or tin containers. Even so, just like all equipment, these securing devices experience common challenges that can affect their overall performance, performance, and the caliber of the covered merchandise. By comprehending and addressing these challenges proactively, beverage companies can preserve ideal device operations, increase productiveness, and supply exceptional packed beverages to buyers. Let's explore several of the popular challenges faced in automatic can closing equipment surgical procedures and methods to get over them.
Seam Problems and Flaws: One of the primary problems in automatic can securing is the appearance of seam problems or flaws, for example loosened seams, creases, or irregularities that undermine close off reliability. To address seam problems, operators should execute standard seam inspections, modify seam moving factors, confirm top location positioning, and enhance strain configurations to achieve steady and trustworthy seals that meet up with quality standards.
Close Integrity and Loss Concerns: Making certain seal integrity and avoiding seepage is crucial in refreshment product packaging to maintain product or service quality, stop toxic contamination, and automatic can sealing machine. To minimize seal off leakage troubles, operators should execute drip screening procedures, verify seam tightness, check atmosphere stress amounts, and perform seal off reliability investigations to determine and resolve possible leakage details before item distribution.
Top Feed and Placement Mistakes: Cover give and positioning errors can bring about sealing errors, cover misalignments, and item wastage in refreshment wrapping operations. To deal with cover feed issues, operators should validate top stock top quality, change top location mechanisms, calibrate top feeders, and monitor lid positioning to guarantee accurate and uniform cover location on cans before sealing, preventing seal problems and refining packaging efficiency.
Machine Routine maintenance and Upkeep: Disregarding routine upkeep, cleaning, and lubrication of automated can sealing models could lead to products wear, decreased overall performance, and potential malfunctions. Manufacturers should establish a extensive routine maintenance timetable, execute typical equipment audits, lubricate moving pieces, replace donned parts, and comply with maker suggestions to prolong machine lifespan, enhance stability, and stop costly fixes.
By acknowledging and addressing these popular difficulties in automatic can securing device procedures, drink manufacturers can preserve operating usefulness, increase merchandise high quality, and maintain creation productivity inside their wrapping functions. Via proactive maintenance, training projects, high quality control measures, and troubleshooting methods, manufacturers can optimize auto can closing machine efficiency, ensure easy production workflows, and deliver substantial-good quality manufactured refreshments that meet up with buyer requirements and business criteria.
related articles:
Guaranteeing Functional Superiority with Auto Can Closing Models
Ensuring that Useful Brilliance with Automatic Can Sealing Gear
Ensuring that Running Excellence with Programmed Can Shutting Styles
Komentarze